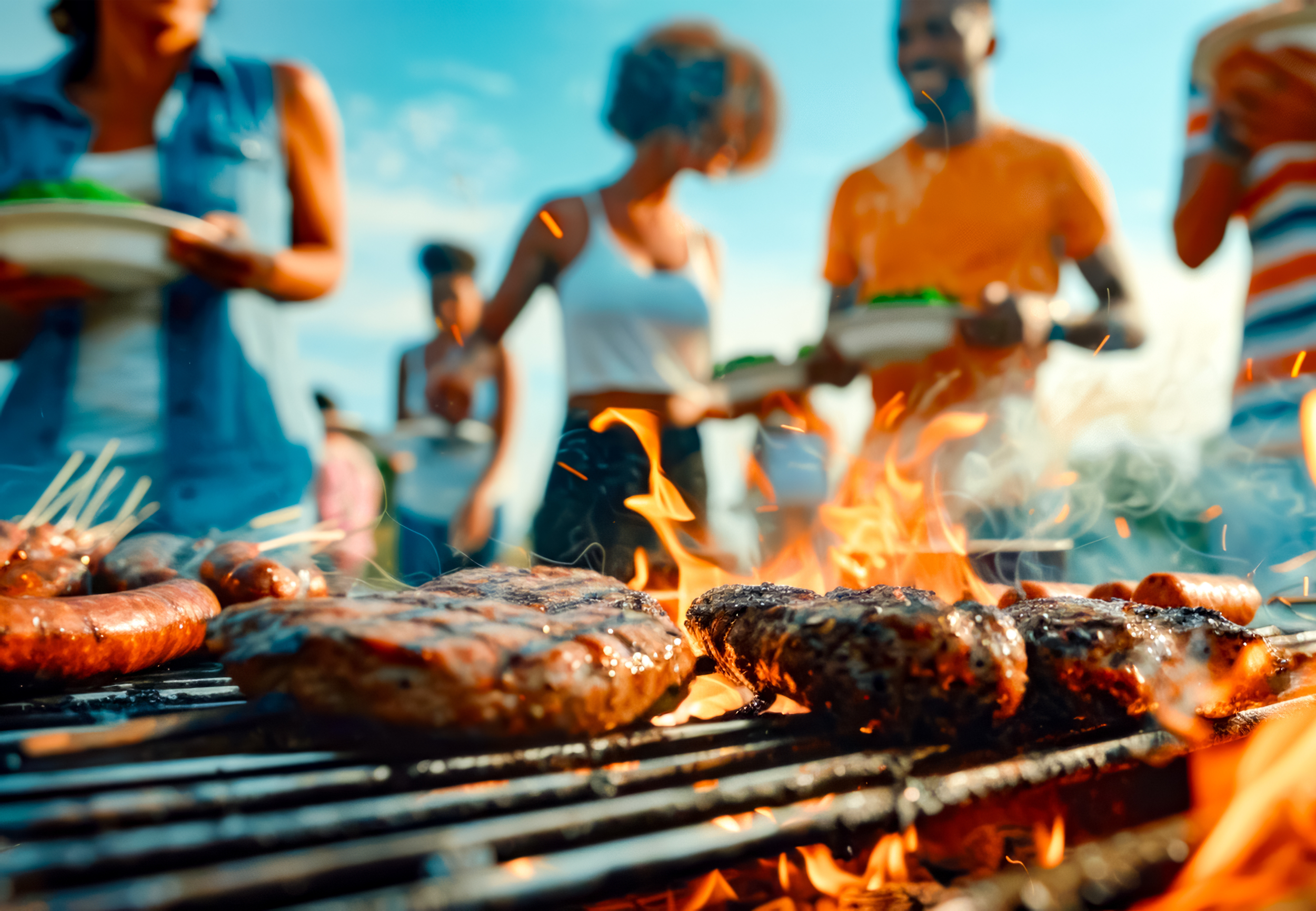
Cultivated Meat Production
Why novel foods need to achieve price parity?
A key factor in cost reduction is the complete replacement of fetal bovine serum (FBS) with recombinant proteins and growth factors, ensuring high-quality cell lines and efficient bioprocesses. However, simply repurposing biopharma/life sciences-derived proteins is not enough—these molecules must be redesigned from the ground up to match the unique needs of cultivated meat production. This requires an approach that is affordable, scalable, and sustainable, moving beyond legacy microbial fermentation methods toward next-generation biomanufacturing solutions.
Unlocking the Future of Cultivated Meat: Overcoming Cost and Production Barriers
Despite significant advancements during the last decade, large investments, and even regulatory approvals, cultivated meat is still far from being a viable alternative to conventional meat. The industry faces two major challenges: high production costs and rigid product expectations. Many early developments aimed to replicate traditional chicken, pork, or beef in taste, texture, and cost—a goal that has proven difficult and continues to hinder broader adoption.
Now, the industry is entering a new phase: shifting from proof-of-concept prototypes to scalable, innovative products designed for industrial production. But to make cultivated meat truly accessible, cost reduction is key, especially when it comes to cell culture media. In the life sciences, media costs can soar to $1,000-$3,000 per liter, while cultivated meat needs to get closer to $1 per liter.
Cultivated muscle tissue
Cultivated fat tissue
Creating a cell biomass with the properties of muscle and fat, involves several components needed to provide the correct instructions and envirornment for the cells. FGF-2 is among the most critical ingredients in cultivated meat production, as it is required for both pluripotent and mesenchymal stem cell expansion. Alongside other growth factors like IGF-1, these proteins support muscle tissue differentiation and fat production -crucial for achieving the desired nutritional values, texture and flavor. Moreover, a recombinant version of bovine albumin is necessary to enhance media performance, enabling the creation of a fully animal-free formulation—a crucial step toward sustainable, cost-effective cell culture for large-scale production.
At Core Bio, we are leading this transition by providing plant-derived, cost-effective, animal-free growth factors and recombinant proteins, optimized for the demands of cultivated meat production. By rethinking these essential components, we are enabling a future where cultivated meat is not just possible, but truly accessible..
Products
-
rbFGF-2 (PL2-50, PL2-1000), food production compatible.
-
rFGF-2 TOP® (PL9-50, PL9-1000), food production compatible.
-
rIGF-1 LR3 (OL11-50, OL11-1000), food production compatible.
-
rEGF, food production compatible.
Core Food Biotech
Animal-free, plant-derived proteins compatible with novel foods
Our team of experts is here to help you optimize your media development
Are you looking for a customized recombinant protein development?
Get in touch to discuss your project and our capabilities